Transforming Metal Fabrication with 3D Printing Prototypes
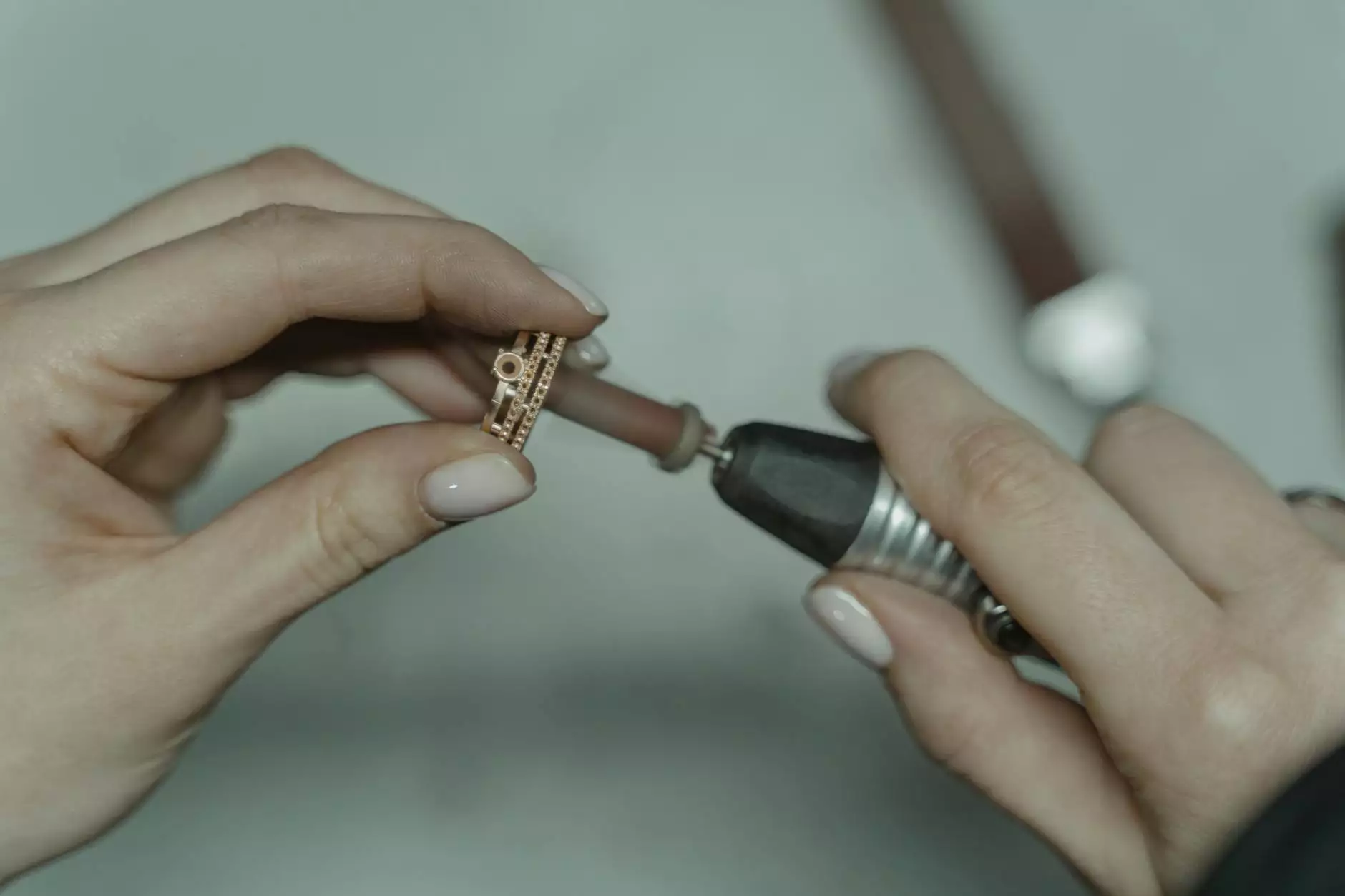
In an era defined by rapid technological advancement, the integration of 3D printing prototypes into the realm of metal fabrication is revolutionizing how businesses operate. Companies like DeepMould.net are leading the charge, utilizing this cutting-edge technology to enhance manufacturing processes, reduce costs, and improve product quality. This article delves into the myriad benefits and applications of 3D printing prototypes in the metal fabrication industry.
Understanding 3D Printing Prototypes
At its core, 3D printing is an additive manufacturing process that constructs objects layer by layer from digital models. When we talk about prototypes, we refer to the preliminary version of a product, a model used to test concepts and designs before full-scale production. The marriage of these two concepts results in 3D printing prototypes, which serve as pivotal tools for businesses in various stages of product development.
The Advantages of Using 3D Printing Prototypes in Metal Fabrication
- Rapid Prototyping: With traditional methods, prototyping can take weeks or even months. 3D printing accelerates this process significantly.
- Cost Efficiency: By minimizing material waste and reducing the need for expensive tooling, 3D printing prototypes lead to substantial cost savings.
- Complex Geometries: Unlike conventional fabrication techniques, 3D printing allows for the creation of intricate designs that were once deemed impossible.
- Material Variety: The ability to use different materials, including metals, polymers, and composites, grants manufacturers versatility in their product designs.
- Design Iteration: 3D printing enables quick design modifications, allowing teams to evaluate several iterations before finalizing a product.
Applications of 3D Printing Prototypes in Metal Fabrication
The applications of 3D printing prototypes in metal fabrication are vast and varied. Here are some prominent uses:
1. Product Development
For manufacturers, 3D printing prototypes plays a crucial role in product development. Designers can create physical models of new products, which allows for better visual and tactile evaluation. This step is vital in gathering feedback from stakeholders and making necessary adjustments before moving to mass production.
2. Tooling and Fixture Creation
Another application is in the creation of customized tools and fixtures. Traditional tooling can be both time-consuming and costly. However, with 3D printing, companies can design and create specialized tools that fit exact specifications, significantly improving assembly line efficiency.
3. Low-Volume Production
For businesses that require low-volume production runs, 3D printing prototypes provides a practical solution. Metal fabrication often involves high costs in tooling for low-volume items, but with 3D printing, companies can effectively produce small quantities economically.
4. High-Performance Parts
Advanced metal 3D printing techniques allow for the production of complex high-performance parts that can withstand extreme conditions, making it ideal for aerospace and automotive industries.
Case Studies Highlighting the Impact of 3D Printing Prototypes
To illustrate the transformative effect of 3D printing prototypes, let’s explore a couple of case studies:
Case Study 1: Aerospace Innovations
A prominent aerospace manufacturer faced challenges in developing lightweight components that could endure high stress. By employing 3D printing technology, the company successfully created complex geometries, resulting in parts that are both lighter and stronger than those made using traditional methods. This innovation led to increased fuel efficiency and reduced emissions, showcasing how 3D printing can propel entire industries forward.
Case Study 2: Customized Medical Devices
A medical device firm used 3D printing prototypes to develop patient-specific implants. By printing the devices tailored to the unique anatomy of each patient, the company improved surgical outcomes and reduced recovery time. This approach not only enhanced patient satisfaction but also solidified the manufacturer’s reputation as a leader in customized medical solutions.
The Future of 3D Printing Prototypes in Metal Fabrication
The future of the metal fabrication landscape is immensely promising with the continued evolution of 3D printing prototypes. Trends suggest a shift towards:
- Increased Availability of Materials: As technologies advance, more metals and composite materials will become accessible for 3D printing, broadening design possibilities.
- Integration with IoT and AI: The fusion of 3D printing with internet of things (IoT) and artificial intelligence (AI) may lead to smarter manufacturing processes where data-driven decisions dictate production methods.
- Sustainability Initiatives: As manufacturers aim for lower environmental impact, 3D printing offers a sustainable alternative by minimizing waste and allowing for the recycling of materials.
How DeepMould.net Is Leading the Charge
With an unwavering commitment to innovation and quality, DeepMould.net is at the forefront of integrating 3D printing prototypes within the metal fabrication sector. The company employs state-of-the-art technology to deliver exceptional products that meet and exceed industry standards. DeepMould's expertise not only streamlines the manufacturing process but also reduces lead times and enhances scalability.
Conclusion
In summary, the incorporation of 3D printing prototypes into metal fabrication is a game-changer. It is reshaping the industry by providing numerous benefits such as rapid prototyping, cost efficiency, and the ability to create complex geometries. As businesses like DeepMould.net harness this powerful technology, the potential for innovation expands, paving the way for advancements that will define the future of manufacturing. The implications of these developments are profound, suggesting a paradigm shift that could redefine production methods across multiple sectors. Embracing 3D printing prototypes is not just a trend; it’s a necessary evolution for any forward-thinking organization aiming to thrive in today’s competitive landscape.