Rapid Prototyping Plastic: Revolutionizing Metal Fabrication
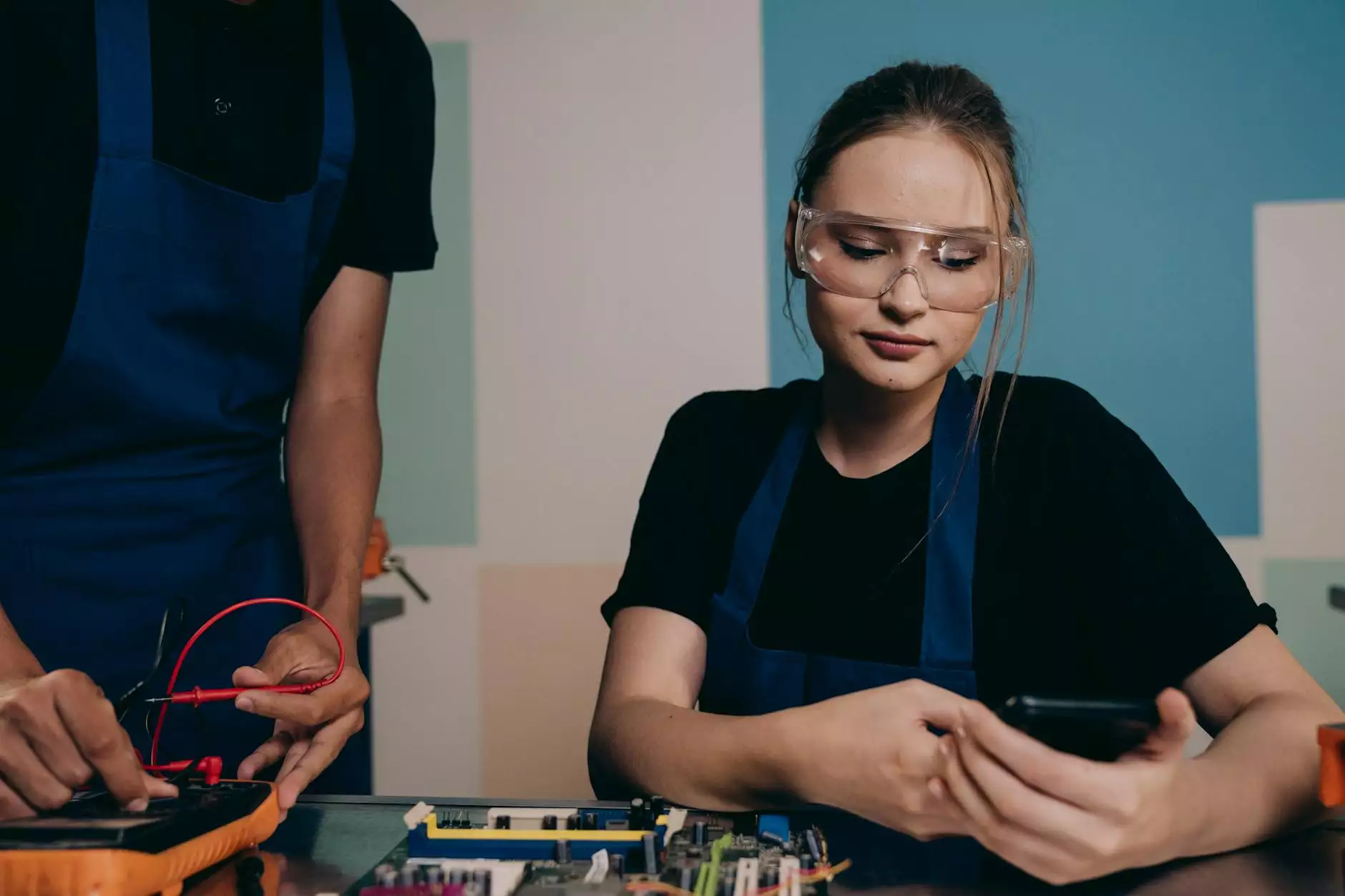
In the rapidly evolving world of manufacturing,rapid prototyping plastic has emerged as an innovative solution that is reshaping traditional practices. Whether you are a small business or a large industrial manufacturer, understanding the significance of rapid prototyping in the context of metal fabrication is essential for staying competitive. This article delves deep into the realm of rapid prototyping plastic, examining its benefits, applications, and the future of the technology in the metal fabrication sector.
Understanding Rapid Prototyping
Rapid prototyping refers to the speedy creation of a physical part or assembly using 3D computer-aided design (CAD) data. The technology allows for swift iterations and testing of designs, aiding manufacturers in identifying potential issues before mass production. One of the most utilized materials in this process is rapid prototyping plastic, favored for its versatility and cost-effectiveness.
The Role of Rapid Prototyping Plastic in Metal Fabrication
In the metal fabrication industry, rapid prototyping plastic serves several key purposes:
- Design Validation: By creating a tangible model of the metal part, designers can visually assess its feasibility and functionality.
- Shortened Production Cycle: Rapid prototyping speeds up the design process, allowing for quicker transitions from conceptualization to production.
- Cost Reduction: Early detection of design flaws can lead to substantial savings by reducing costly changes during mass production.
- Enhanced Collaboration: Prototypes enable better communication among teams, ensuring that all stakeholders are on the same page before production begins.
Benefits of Rapid Prototyping Plastic
Utilizing rapid prototyping plastic within the metal fabrication process provides various advantages:
1. Speed
One of the primary benefits of rapid prototyping is the speed at which prototypes can be developed. Traditional methods could take weeks or even months, whereas rapid prototyping can yield results in a matter of days. This fast turnaround time encourages innovation and allows businesses to respond quickly to market demands.
2. Cost-Effectiveness
Producing prototypes using rapid prototyping plastic is generally more affordable than crafting models out of metal. The reduction in material costs, combined with less time spent on creation, translates to a more economical process overall.
3. Flexibility and Versatility
Plastic materials are adaptable and can be easily modified or transformed to meet specific design requirements. This flexibility allows engineers to experiment with different shapes and sizes, aiding in the exploration of multiple design options.
4. Improved Accuracy
Modern rapid prototyping techniques, such as Stereolithography (SLA) and Fused Deposition Modeling (FDM), provide high precision, resulting in prototypes that closely resemble the final product. This improved accuracy minimizes the risk of errors when transitioning to metal fabrication.
Applications of Rapid Prototyping Plastic in Metal Fabrication
Numerous industries can benefit from utilizing rapid prototyping plastic in their metal fabrication processes. Below are a few notable applications:
- Aerospace Industry: Rapid prototyping allows for the testing of intricate designs before they are implemented into aircraft, where safety and efficiency are paramount.
- Automotive Manufacturing: Car manufacturers use rapid prototyping to create components and assemblies that require rigorous testing, ensuring all parts function together seamlessly.
- Medical Devices: In the medical field, rapid prototypes of surgical tools or prosthetics can be created for testing and approval, accelerating the time to market.
- Consumer Products: Brands use rapid prototyping to design innovative products and gather user feedback, allowing for adjustments before full-scale production.
How Rapid Prototyping Plastic Works
The process of creating prototypes using rapid prototyping plastic typically follows these stages:
- Design Creation: A CAD model is generated, which acts as the blueprint for the prototype.
- Material Selection: Based on the intended use, the appropriate plastic material is chosen from options like ABS, PLA, or nylon.
- Printing or Molding: The prototype is created through 3D printing or injection molding, depending on the design and complexity.
- Post-Processing: Once printed, the prototype may undergo finishing processes such as sanding or painting to achieve the desired appearance.
Future Trends in Rapid Prototyping Plastic
As technology continues to advance, several trends are expected to influence the future of rapid prototyping plastic in metal fabrication:
1. Advanced Materials
Development of new materials that mimic the properties of metals will enhance the capabilities of rapid prototyping. These advanced plastics will offer strength, durability, and heat resistance, making them suitable for more demanding applications.
2. Integration with AI and Machine Learning
Artificial intelligence and machine learning algorithms can analyze design data and recommend optimizations, leading to better prototyping outcomes. Integrating AI will streamline the prototyping process further, allowing for greater efficiency.
3. Customization and Personalization
As consumer demands shift towards personalized products, rapid prototyping will facilitate the production of customized components on a larger scale.
4. Sustainability
With a growing emphasis on environmentally friendly practices, the development of biodegradable and recyclable rapid prototyping plastics will play a significant role in the industry’s future.
Conclusion
In summary, rapid prototyping plastic represents a paradigm shift in metal fabrication. By offering speed, cost-effectiveness, flexibility, and precision, it enables manufacturers to innovate and adapt in an ever-changing marketplace. The endless possibilities of its applications, combined with emerging technologies and materials, ensure that rapid prototyping will remain a cornerstone of modern manufacturing. For businesses aiming to stay competitive and responsive to market demands, embracing rapid prototyping technology is essential.
To explore further how rapid prototyping plastic can elevate your manufacturing processes, consider partnering with experts such as DeepMould.net, a leader in the field. Their expertise in metal fabrication and rapid prototyping can guide you through the transformative journey ahead.