Maximizing Efficiency with Volumetric Concrete Plants
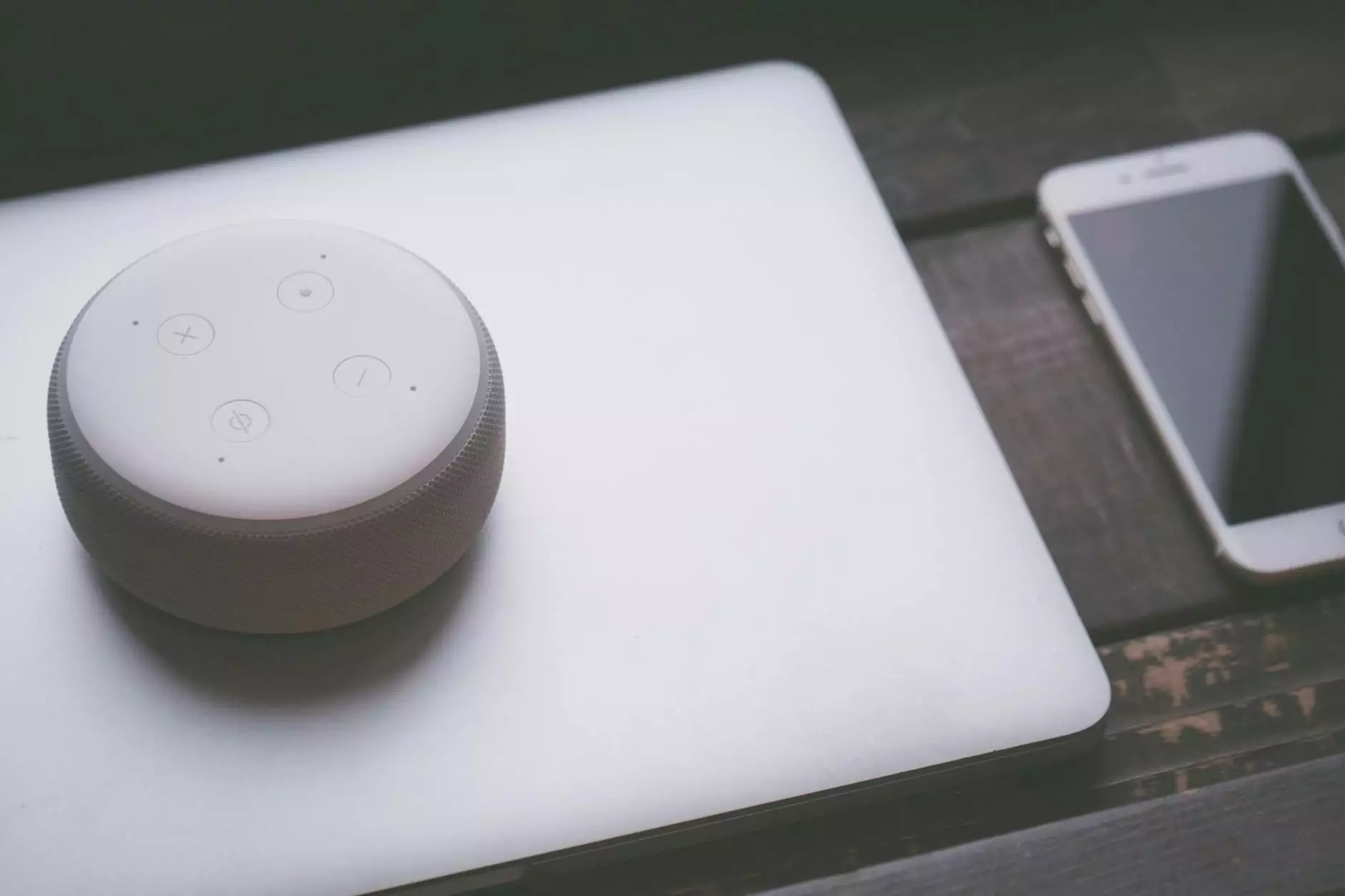
In the construction industry, efficiency and sustainability are paramount. One significant innovation that has revolutionized concrete production is the use of volumetric concrete plants. This advanced technology allows for precise, on-demand concrete mixing, catering specifically to the needs of various projects. Companies like Polygonmach play a crucial role in manufacturing these state-of-the-art plants, ensuring that businesses can maximize their operational efficiency.
Understanding Volumetric Concrete Plants
A volumetric concrete plant is a mobile concrete mixer that combines raw materials like cement, sand, and aggregates in the precise proportions required for concrete mixing. Unlike traditional batch plants, volumetric mixers operate by measuring the materials by volume rather than weight, ensuring accuracy and consistency. Let’s delve deeper into how these machines operate and the benefits they provide to modern construction projects.
How Do Volumetric Concrete Plants Work?
At the core of a volumetric concrete plant is its unique mixing system. This system includes several key components:
- Cement Silos: Store the cement and discharge it into the mixer as needed.
- Aggregate Bins: Hold sand and gravel, allowing for easy dispensing.
- Water Supply: Essential for creating the right mixture consistency.
- The Mixer: Where the materials are combined in real-time to produce fresh concrete.
The volumetric concrete mixer continuously measures and mixes the components to achieve the desired concrete mix. This means operators can produce various concrete types without waiting for a batch to finish; they can adjust the formulation on the fly, enhancing productivity on site.
Key Advantages of Volumetric Concrete Plants
The adoption of volumetric concrete plants presents numerous advantages for construction businesses. Here are some compelling benefits:
1. Cost Efficiency
With traditional batching plants, there are often delays caused by waiting for predetermined amounts of concrete, which can lead to wastage. In contrast, volumetric systems minimize both waste and downtime:
- Reduced Waste: Only the amount of concrete needed is mixed at any given time.
- Lower Transportation Costs: These plants are mobile, enabling concrete production right at the job site.
2. Flexibility and Customization
Each construction project is unique, and the ability to customize concrete mixtures is paramount. Volumetric concrete plants provide:
- On-Demand Mixing: Adjustments can be made to the mix design depending on specific project requirements.
- Variety: The capability to produce different concrete types without reconfiguring the plant.
3. Enhanced Quality Control
Since concrete is mixed on-site, there’s greater control over the quality of the materials used:
- Freshly Mixed Concrete: Eliminates issues with setting time and consistency associated with pre-mixed, delivered concrete.
- Real-Time Adjustments: Changes can be made if the material quality is not meeting standards.
4. Sustainability Benefits
The construction industry faces increasing pressure to adopt sustainable practices. Volumetric concrete plants contribute to eco-friendliness through:
- Reduced Carbon Footprint: Minimizes transportation and associated emissions.
- Efficient Resource Use: Only necessary materials are utilized, reducing waste.
Applications of Volumetric Concrete Plants
Volumetric concrete plants are versatile and applicable in various construction contexts:
1. Residential Construction
For homebuilders, volumetric mixers provide customizable concrete solutions, whether for foundations, driveways, or decorative elements.
2. Commercial Projects
In commercial applications, the ability to mix large batches of concrete quickly enhances productivity, essential for meeting tight project deadlines.
3. Infrastructure Development
From roads to bridges, volumetric concrete plants ensure that infrastructure projects can proceed without delays caused by concrete shortages.
Choosing the Right Volumetric Concrete Plant
Investing in a volumetric concrete plant is a significant decision for any construction company. Here are factors to consider:
- Capacity: Choose based on the scale of projects and expected concrete volume.
- Mobility: Consider whether you need a portable solution or a fixed plant.
- Customization Options: Ensure the plant can handle specific mix designs relevant to your projects.
- Support and Maintenance: Partner with reputable manufacturers like Polygonmach for ongoing service and support.
Best Practices for Operating Volumetric Concrete Plants
To maximize the efficiency and effectiveness of your volumetric concrete plant, adopt these best practices:
1. Regular Maintenance
Routine checks are vital to ensure optimal performance. This includes monitoring wear and tear on the mixing components and verifying calibration.
2. Training Operators
Ensure that all personnel operating the volumetric concrete plant are well-trained in its functions, controls, and maintenance requirements.
3. Accurate Material Sourcing
The quality of your concrete mixture directly depends on the quality of the raw materials used. Invest in high-quality cement, aggregates, and additives.
Conclusion
As the construction industry moves towards improved efficiency and sustainability, incorporating a volumetric concrete plant into your operations can have profound benefits. From reducing waste to enabling precise, on-demand mixing, these innovative plants pave the way for modern construction practices. By partnering with trusted manufacturers like Polygonmach, companies can invest in cutting-edge technology that enhances their competitive edge in the marketplace.