Understanding Titanium Tube Fittings: A Comprehensive Guide
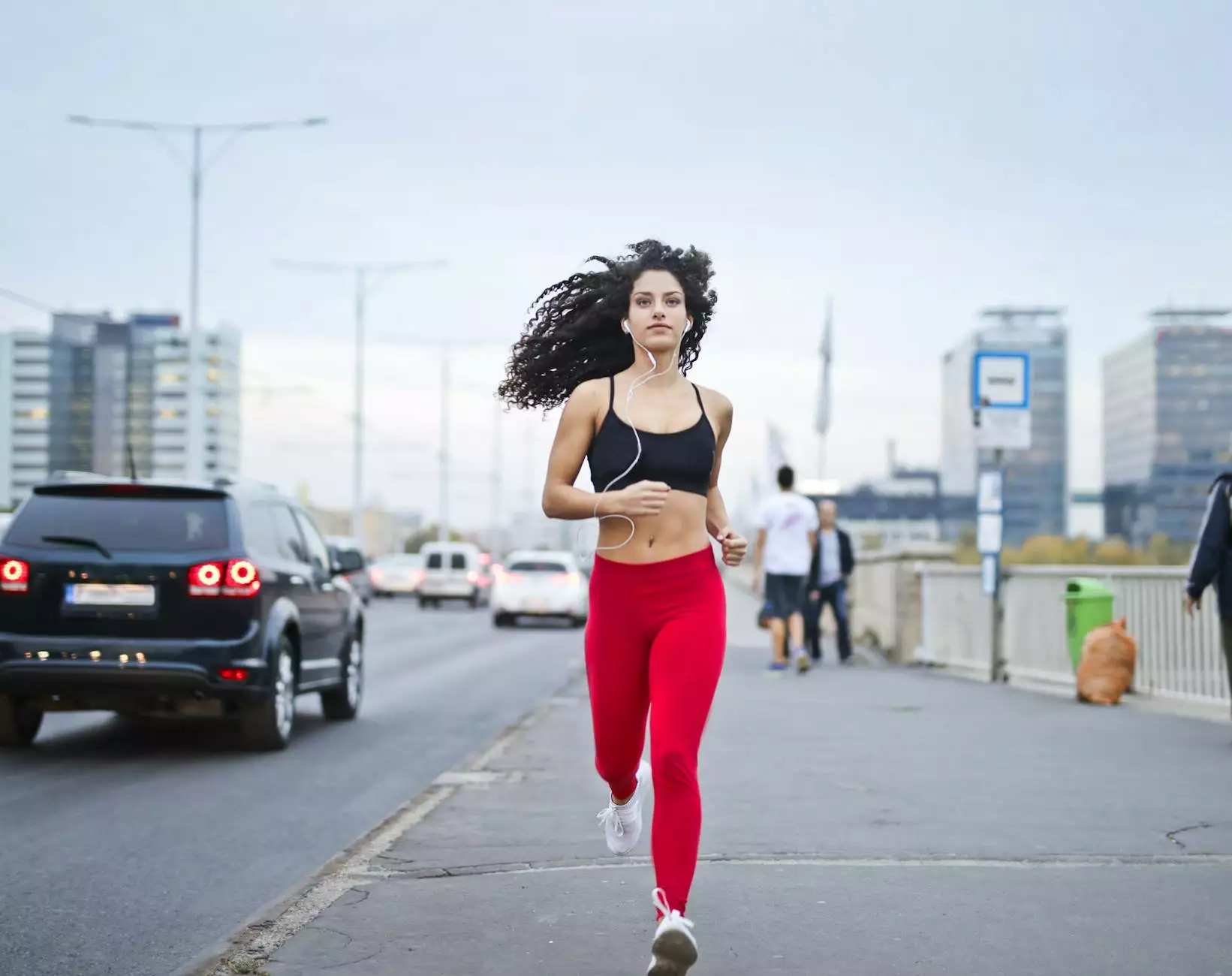
Titanium tube fittings are crucial components in a wide range of industrial applications. Renowned for their strength, durability, and resistance to corrosion, these fittings are becoming increasingly popular in various sectors, including aerospace, chemical processing, and oil and gas. In this article, we will delve deep into the world of titanium tube fittings, discussing their properties, advantages, manufacturing processes, and applications.
The Magic of Titanium
Titanium is a transition metal known for its impressive strength-to-weight ratio and remarkable resistance to corrosion. As one of the strongest metals, titanium exhibits excellent performance even in the most demanding environments. This metal is found at the core of many advanced engineering solutions across different industries.
The Importance of Tube Fittings
Tube fittings play a significant role in ensuring the efficiency and safety of fluid and gas transport systems. They connect various components of a piping system, maintaining a secure and leak-free operation. When it comes to materials, titanium tube fittings dominate owing to their unique properties.
Properties of Titanium Tube Fittings
- Corrosion Resistance: Titanium withstands harsh environments, including salty and acidic conditions.
- High Strength: The tensile strength of titanium surpasses that of many metals, which means it can handle high pressure without deforming.
- Lightweight: Titanium is significantly lighter than steel, making it easier to handle and transport.
- Biocompatibility: Titanium is non-toxic and compatible with the human body, making it ideal for medical applications.
- Heat Resistance: Titanium retains its properties at elevated temperatures, essential for high-temperature applications.
Types of Titanium Tube Fittings
Titanium tube fittings come in various forms to cater to different needs. Below are some of the most commonly used types:
1. Single Ferrule Tube Fittings
Single ferrule fittings are designed to provide a reliable seal with minimal assembly effort. They are ideal for applications where space is a constraint.
2. Double Ferrule Tube Fittings
Double ferrule fittings offer enhanced leak protection and are suitable for high-pressure and temperature applications. They provide a more secure grip compared to single ferrule fittings.
3. NPT (National Pipe Thread) Fittings
NPT fittings are designed to connect pipes through a threaded connection. They are widely used in hydraulic and pneumatic systems.
4. Forged Pipe Fittings
Forged fittings are created through a specific manufacturing process that enhances their strength. These fittings are often used in high-pressure applications.
5. Flanges
Flanges are used to connect pipes, valves, and pumps. They allow for easy maintenance and inspection.
Advantages of Using Titanium Tube Fittings
The transition to titanium tube fittings offers manufacturers and engineers numerous benefits. Here are the key advantages:
- Longevity: Their durability translates to a longer lifespan, reducing the need for frequent replacements.
- Cost-Effectiveness: While the initial cost may be higher, the reduced maintenance and replacement costs over time make titanium fittings a wise investment.
- Reduced Weight: The lightweight nature decreases the overall load on structures and support systems, enhancing design flexibility.
- Compatibility: Titanium's non-reactive nature allows it to be used with a wide range of fluids and gases without the risk of contamination.
- Reliability: They provide secure and leak-free connections that minimize system failures and downtime.
Applications of Titanium Tube Fittings
Titanium tube fittings find applications across various industries, including:
Aerospace Industry
In aerospace, weight savings coupled with high strength are critical. Titanium tube fittings are used in hydraulic systems, fuel systems, and airframe structures to ensure both reliability and performance.
Chemical Processing
Due to their resistance to corrosive substances, titanium fittings are utilized in chemical processing plants, where they help in handling aggressive chemicals safely.
Oil and Gas Exploration
The oil and gas industry demands fittings that can withstand extreme conditions. Titanium fittings are used in high-pressure pipelines and offshore platforms.
Medical Applications
Titanium's biocompatibility allows it to be used in various medical devices, including surgical instruments and implants. Tube fittings ensure secure connections in biofluid transport systems.
Marine Applications
In marine environments, titanium tube fittings resist saltwater corrosion, making them ideal for boat and ship manufacturing.
Manufacturing Process of Titanium Tube Fittings
The manufacturing process of titanium tube fittings involves several critical steps:
1. Material Selection
The first step is selecting high-quality titanium alloys that will provide the necessary strength and corrosion resistance for specific applications.
2. Machining
Titanium is worked using precision machining techniques that minimize waste and ensure high-quality finishes. This step involves turning, milling, and drilling the material into desired shapes.
3. Forging
Some fittings are manufactured through a forging process that enhances their strength and structural integrity. This process involves shaping the titanium under high pressure.
4. Heat Treatment
Heat treatment can be applied to titanium components to improve their mechanical properties further, ensuring optimal performance in demanding conditions.
5. Quality Control
Every batch of titanium tube fittings undergoes rigorous testing to ensure they meet industry standards. This includes pressure testing, visual inspections, and material analysis.
Choosing the Right Titanium Tube Fittings
When selecting titanium tube fittings, consider the following factors:
- Application Requirements: Understand the specific pressures, temperatures, and fluids involved in your application.
- Compatibility: Ensure the fittings are compatible with the materials and systems they will connect to.
- Certification Standards: Verify that the fittings meet necessary industry standards and certifications.
- Supplier Reputation: Choose a supplier known for manufacturing high-quality titanium products, such as TechTubes.
Conclusion
In conclusion, titanium tube fittings are becoming increasingly vital in modern engineering due to their unique properties, such as strength, durability, and corrosion resistance. From aerospace to chemical processing, these fittings provide reliable solutions for fluid and gas transport systems. As industries evolve and demand for advanced materials grows, titanium tube fittings will undoubtedly maintain their role as a preferred choice for engineers and manufacturers alike.
For businesses looking to improve their systems' efficiency and longevity, investing in high-quality titanium tube fittings is not just a choice; it is a necessity. Embrace the future of engineering with titanium solutions that stand the test of time.